In June 2024, The team of Professor Feng Qingge from SKL is entitled "Integrated use of Bayer red mud and electrolytic manganese residue in limestone calcined clay cement (LC3) via thermal treatment activation" was published in the Journal of Building Engineering.
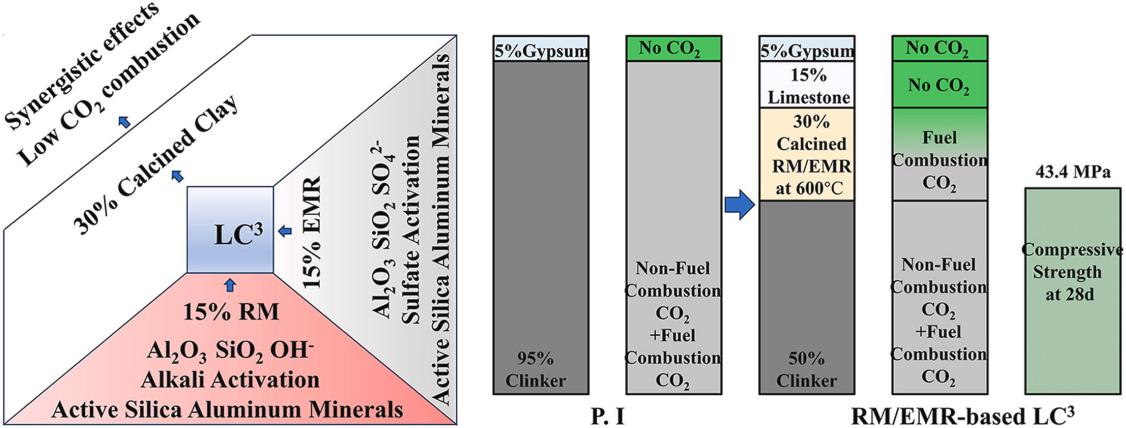
Limestone calcined clay cement (LC3) is a crucial low-carbon alternative for the future of the cement industry. Bayer red mud (RM) and electrolytic manganese residue (EMR), byproducts of aluminum and manganese production, respectively, pose significant environmental challenges due to their high volume and hazardous components. Utilizing these materials in LC3not only mitigates disposal issues but also leverages their rich content of Al2O3and SiO2, which resemble the properties of calcined clay after thermal treatment. This study investigates the mixture of RM and EMR with cement clinker, limestone powder, and gypsum to create a cementitious material with low carbon emissions. It examines the impact of thermal treatment temperature on RM and EMR reactivity and determines the optimal mix design. The findings indicate that the ideal thermal treatment temperature is 600 °C, with a 1:1 RM to EMR ratio, achieving the best mechanical properties and synergistic effects. The compressive strength of the RM/EMR-based LC3reached 43.4 MPa at 28 days with a water-to-cement ratio of 0.35. Microstructural analysis reveals that RM, EMR, and limestone powder react to form monocarboaluminate in a calcium hydroxide-induced alkaline environment. Active Al2O3and SiO2in the RM and calcium sulfate in the EMR facilitate a secondary hydration reaction. The cementitious material, prepared from thermally activated RM and EMR, can potentially reduce CO2emissions by 26.2 % and energy consumption by 14.9 % per ton compared to conventional Portland cement. This study demonstrates a sustainable approach for the cement industry, offering a viable solution for waste management and carbon reduction.